Blog Post
The Evolution of Beer Bottling Crate Inspection Technologies: From Manual to AI Inspection
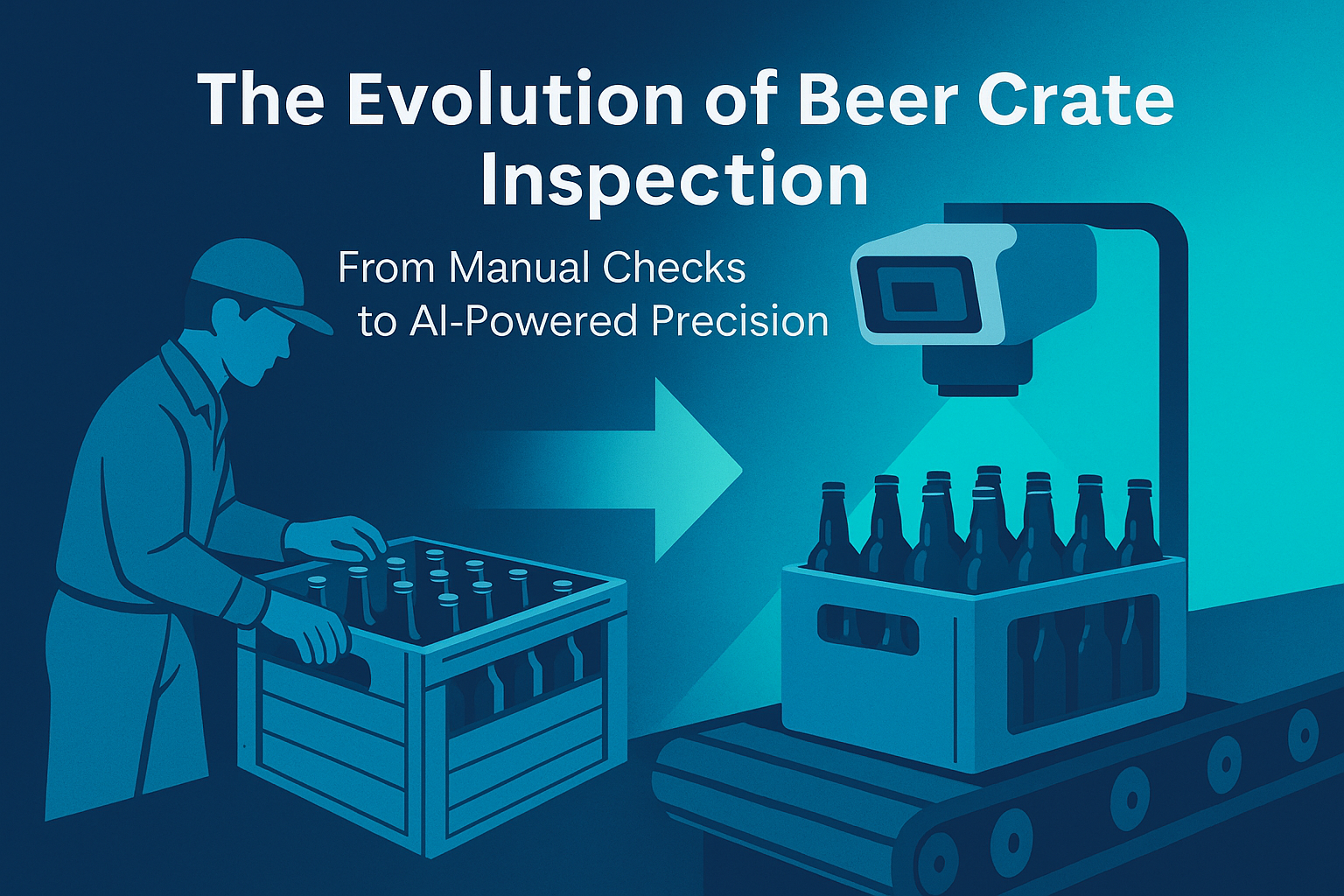
For decades, beer brewing companies have always needed to inspect bottles and crates before they are shipped off to customers for consumption. Over time, the last 2 decades to be specific, crate inspection and assessment technology has shifted from basic manual checks by humans, to sonar sensors, to AI being implemented as a form of computer vision.
This evolution has been driven by the need for greater efficiency, accuracy, and quality in the brewing industry, where the correct composition and condition of crates are essential for seamless production and customer satisfaction. Poor crate inspection at a brewery could lead to a high percentage of refunds or replacements of bottles for customers. Poor crate inspection can easily lead to the end of a brewery's brand and its preference among alcohol resellers.
Early Manual Inspection
Traditionally, the inspection of beer crates was a manual process. Workers visually checked crates as they moved along conveyor belts, ensuring each crate contained the correct number and type of bottles. This approach was labor-intensive, slow, and prone to human error. In fact, it was estimated that over a third of bottles arriving at breweries were in the wrong crate, leading to significant inefficiencies and potential quality issues.
Introduction of Basic Sensors
To improve reliability, breweries began integrating standard sensor technologies. These early systems used multiple individual sensors to detect the presence or absence of bottles in crates. While this represented a step forward, such systems were often complex, inflexible, and struggled to adapt to varying crate and bottle types, requiring frequent manual adjustments.
Emergence of Machine Vision and Intelligent Sensors
The next major leap came with the adoption of machine vision systems and intelligent image-based sensors. For example, the Ottakringer Brauerei in Vienna implemented Cognex’s Checker 101 vision sensor to automate the inspection of beer crates and can cases. This compact sensor could analyze up to 500 images per second, distinguishing between different bottle types and ensuring crate completeness without manual intervention. The system’s flexibility allowed for quick reprogramming via a laptop, enabling efficient adaptation to different packaging formats and reducing downtime.
Adoption of Laser Scanners
Recent years have seen the rise of non-contact laser scanning technology for crate inspection. Companies like Tipteh have developed systems utilizing laser line triangulation sensors, such as the scanCONTROL 2900-50 from Micro-Epsilon. These scanners measure crates from above as they travel along conveyor belts, detecting both the presence and height of each bottle. This allows not only for completeness checks but also for verifying that the correct bottle type is in the crate, as even minor deviations in height (greater than 3 mm) are flagged. The results are processed in real time by programmable logic controllers, which can automatically remove faulty crates from the production line.
Compared to conventional image processing, laser scanners offer higher speed, accuracy, and reliability, even on the fastest production lines. They also provide seamless integration with existing control systems and display measured results directly to operators, further streamlining the process.
High-Speed Machine Vision Systems
At the cutting edge, high-speed machine vision systems like the SpeedView, developed by R&D Vision, use advanced cameras and software to inspect bottles at rates of up to 1,000 frames per second. These systems can record, analyze, and trigger maintenance actions without stopping production, minimizing costly downtime and enabling near-zero failure rates. Such solutions are portable, quick to set up, and offer detailed frame-by-frame analysis for maintenance teams.
FirstStep's Full Crate Inspector Compared To Modern-day Crate Inspectors
For senior brewery operations leaders evaluating inspection solutions, the comparison below highlights how FirstStep.AI’s Full Crate Inspector (FCI) outperforms conventional crate inspection systems (e.g. HEUFT LKX, JLI Vision, Vision-Tec, BBULL) in key areas. These differences directly impact line throughput, uptime, and long-term quality traceability:
Feature | FirstStep.AI Full Crate Inspector (FCI) | Conventional Crate Inspection Systems |
---|---|---|
Deployment & Throughput | Non-invasive overhead system (no conveyor modifications); inspects up to 7,200 crates/hour per unit with dual-lane support (≈3,600 crates/hour per lane). | In-line installation often requires a special conveyor section or sensors; typically handles ~4,000–6,000 crates/hour per unit on a single lane. |
Data Archiving & Traceability | Central image archive stores every crate inspection for audits & traceability; enabling comprehensive long-term tracking of crate quality. | Limited archiving (often only fault logs or snapshots); traceability features are basic and not centralized, providing far less historical insight. |
Interface & Flexibility | User-friendly interface with real-time, shift-level reports firststep.ai accessible to staff; automatically adapts to different crate brands or designs without manual re-teaching; open integration (OPC UA/SCADA support) for seamless connectivity. | On-site HMI with basic displays; any new crate type or logo change requires manual teaching/setup by an operator (no auto-adjustment); integration and remote access are limited compared to modern standards. |
Throughput, Multi-Lane Capacity, and Easy Deployment: FirstStep.AI’s FCI stands out in sheer throughput and deployment efficiency. It can inspect up to 7,200 crates per hour with a dual-lane setup, comfortably outpacing legacy systems that top out around 4,000–6,000 crates/hour on a single lane. In practical terms, this higher scan rate means the FCI can keep up with the fastest bottling lines without becoming a bottleneck. Moreover, one FCI unit can cover two parallel crate lanes at once, whereas conventional solutions generally require one separate inspector per lane. This not only boosts total throughput per unit, but also simplifies scaling to additional lines. Installation is also far less disruptive – FCI’s overhead camera design eliminates the need to cut into conveyors or add complex line machinery. Brewers can mount the system above existing belts with minimal downtime, preserving valuable uptime. Traditional crate inspectors, by contrast, often demand dedicated conveyor modifications or special vision tunnels, which increase installation time and can cause production stoppages. By providing higher capacity in a single device and a drop-in installation, FCI maximizes operational throughput and minimizes integration hassles – a combination that translates to more runtime and efficiency for busy packaging halls.
Robust Archiving for Complete Traceability: Another major advantage of the FCI is its built-in archival capabilities for quality control. Every inspected crate’s images and data are automatically saved to a central repository, creating a detailed digital “paper trail” of packaging quality over time. This means that if a question ever arises about a particular crate or batch, brewery quality teams can easily pull up the exact inspection images and results for verification. The long-term traceability offered by this archive is a game-changer for breweries – it supports root cause analysis (for example, tracing recurring crate defects back to a specific supplier or line issue) and provides hard evidence for audits or customer inquiries. Most legacy systems lack this depth of record-keeping. Conventional inspectors might only log basic pass/fail counts or save a handful of fault images, offering nowhere near the comprehensive historical insight of FCI. In contrast, FirstStep.AI’s solution essentially creates a “crate logbook” for every production shift, which is invaluable for compliance and continuous improvement initiatives. For senior quality and process managers, this translates into greater confidence and accountability – every crate’s journey is documented, enabling data-driven decisions to enhance packaging quality and reliability in the long run.
Accessible Interface and Operational Flexibility: The FCI also excels in user interface and system flexibility, making it particularly appealing to operations-focused leaders. Its interface is modern and highly accessible, presenting real-time metrics and customizable reports that packaging and production managers can easily interpret. Instead of relying solely on a local machine display, FCI can integrate with brewery networks and software, so supervisors can monitor crate inspection performance from the control room or even remotely. Equally important, the system’s AI-powered adaptability means it requires little manual intervention when conditions change. For instance, if the brewery switches to a different crate type or brand logo, the FCI can automatically adjust to the new appearance without needing an engineer to pause the line and reprogram it. This kind of flexibility sharply reduces changeover downtime and ensures inspection doesn’t miss a beat as production varies. Traditional crate inspectors, in comparison, often require operators to manually “teach” the system how to recognize each new crate design or acceptable variation. Every brand change or new crate introduction can entail time-consuming calibration on those older systems, during which the line might need to slow or stop. Additionally, legacy interfaces tend to be less friendly for advanced data analysis or remote access, limiting how easily teams can extract insights. FirstStep.AI’s FCI, on the other hand, was built with connectivity in mind – it offers straightforward integration into existing SCADA/PLC systems via standards like OPC UA, enabling its data and alerts to feed into the broader brewery control system. This interface accessibility and integration flexibility mean that brewery leadership can rely on FCI as a transparent, adaptable part of the production line. In day-to-day terms, teams can respond faster to any issues (with live alerts and intuitive dashboards), scale the inspection to new lines or products without headache, and continuously improve the process using rich data. The result is a more agile and efficient operation, where high quality is maintained with less effort – a clear competitive edge over the more rigid, traditional inspection setups.
Where Is Beer Bottle Crate Inspection Technology Heading Over The Next Decade?
The ongoing transformation of beer bottle crate inspection technology exemplifies the beverage industry's broader push toward intelligent automation and precision-driven quality control. Transitioning from traditional manual inspections toward AI-powered, high-speed inspection systems, breweries are increasingly equipped to deliver consistently high-quality products, minimize operational downtime, and optimize efficiency. Modern inspection systems, such as FirstStep.ai's Full Crate Inspector, exemplify this shift by offering advanced features like dual-lane, high-throughput scanning, easy installation, and robust image archiving capabilities for thorough, long-term traceability.
Looking ahead, the future of crate inspection clearly points toward enhanced automation characterized by AI-driven adaptability, seamless integration with broader production control systems, and real-time analytics. Solutions will likely evolve to automatically handle brand changes and new crate designs effortlessly, significantly reducing downtime associated with manual recalibrations. The emphasis will increasingly shift from physical intervention to overseeing sophisticated AI algorithms capable of continuous self-improvement and predictive defect detection.
Ultimately, breweries adopting these advanced technologies will benefit not only from immediate operational improvements but also from enhanced long-term data insights that support smarter, proactive decision-making. As AI continues to advance, beer crate inspection will become increasingly autonomous, transforming brewery workflows and setting new standards for efficiency, reliability, and product quality.