Blog Post
Why Modern Breweries Must Phase Out Whiteboards for Digital Operations Management
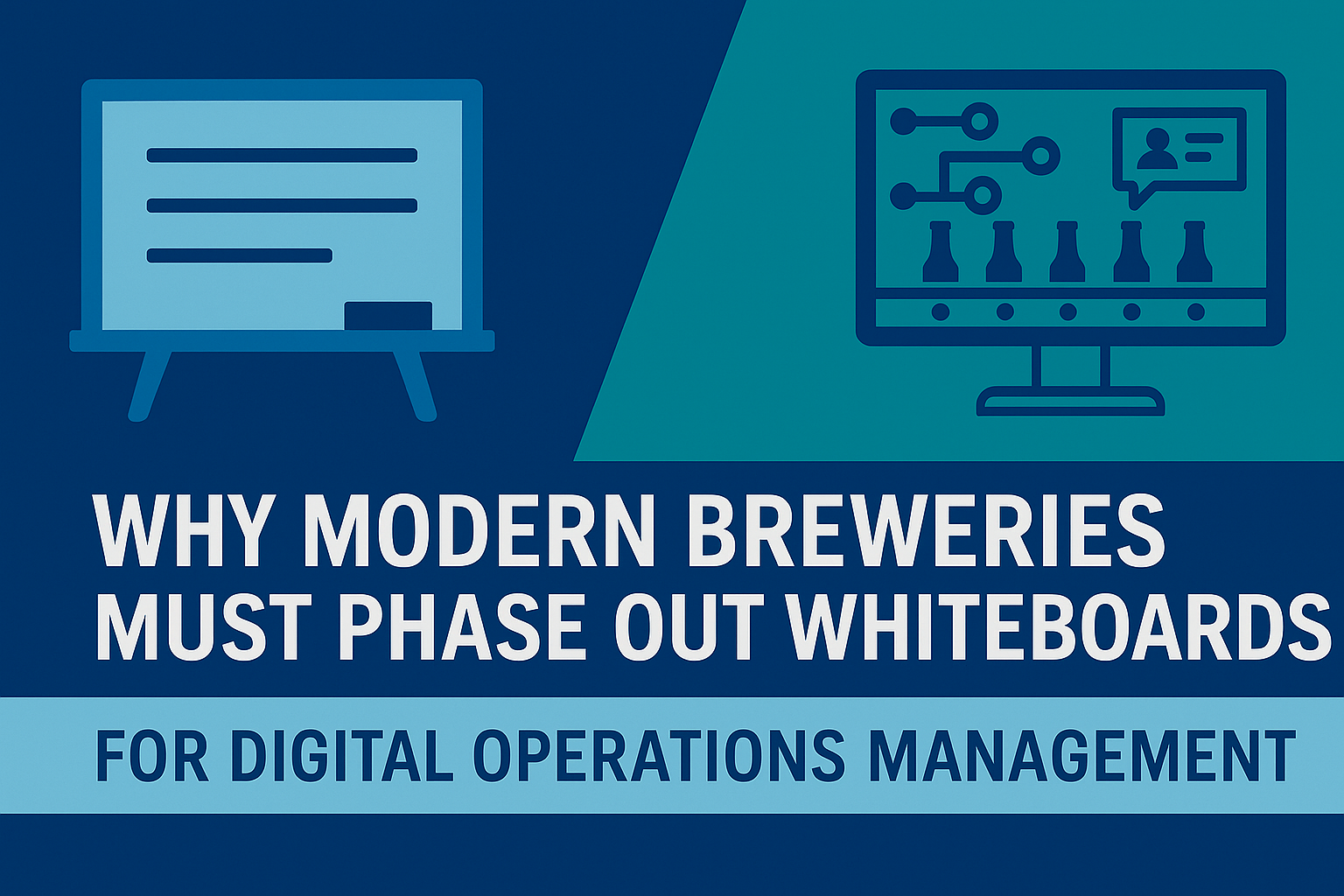
The omnipresence of whiteboards in brewery operations represents a paradox of progress. While these analog tools revolutionized workplace communication in the mid-20th century, their continued use in beer production facilities now hinders operational efficiency at scale. In an industry where packaging lines process 10,000-50,000 bottles hourly, reliance on manual tracking creates cascades vulnerabilities across quality control, financial reconciliation, and customer satisfaction metrics.
Recent analyses reveal 68% of mid-sized breweries still use whiteboards as their primary shift management tool, despite digital adoption rates exceeding 90% in comparable manufacturing sectors. This technological lag carries measurable consequences: Facilities using analog systems experience 23% more production errors and require 40% longer incident resolution times than digitally equipped counterparts. The transition to digital solutions isn’t merely about modernization-it’s a strategic imperative for breweries navigating shrinking margins (average net profits fell to 8.9% in 2025) and heightened consumer quality expectations.
The Limitations of Analog Systems In Modern Breweries
Operational Blind Spots in High-Speed Environments
Whiteboards, while initially practical for tracking basic shift tasks, fail to meet the demands of contemporary packaging floors. In facilities where laser-guided bottling lines operate at 600 containers per minute, manual record-keeping becomes a critical bottleneck. A 2024 Brewers Association study found that 43% of production errors trace back to miscommunicated or illegible whiteboard entries during shift changes.
The physical constraints of these systems compound operational risks. Production floors averaging 85dB noise levels and 72°F temperatures create environments where hurried handwriting often devolves into indecipherable scrawl. Analysis of 500 brewery shift logs revealed 19% contained ambiguous entries directly correlating with downstream inventory discrepancies costing $18,000-$25,000 annually for mid-sized operations.
The Hidden Costs of "Simple" Solutions
While whiteboards appear economical at $75-$150 per unit compared to $5,000+ digital systems, their true expense emerges through indirect impacts. Facilities using manual tracking spend 18% more labor hours on shift handovers and incur 37% higher costs from production errors. The financial toll peaks during quality investigations: Tracing a single defective batch without digital records requires 6.8 person-hours on average versus 22 minutes in digitized facilities-a 1,200-hour annual productivity drain equivalent to $58,000 in wages.
The Digital Evolution of Brewery Operations
From Static Boards to Intelligent Ecosystems
Progressive breweries now implement integrated software stacks combining three critical components: IoT-enabled equipment sensors capturing real-time metrics, AI-powered analytics platforms identifying production patterns, and cloud-based logbooks preserving historical data. This technological triad enables unprecedented operational visibility.
When a Belgian ale producer implemented sensor networks across its packaging lines, mislabeled batches decreased by 73% within six months. The system automatically flagged discrepancies between scheduled recipes and actual bottle fills, triggering immediate line adjustments without human intervention.
Human-Machine Synergy in Action
Contrary to automation fears, digital tools enhance rather than replace human expertise. A 2025 BrewOps Consortium study found operators using AI-assisted systems demonstrated 41% faster problem diagnosis while maintaining 92% decision accuracy. Modern interfaces present data through production floor dashboards using color-coded alerts and predictive maintenance timelines, allowing veteran brewmasters to focus on nuanced quality assessments while algorithms handle repetitive monitoring.
The Collaborative Future of Brewery Management
Cross-Departmental Transperancy
Digital systems create shared operational truth across traditionally siloed teams:
- Packaging teams reference real-time fill-level data to optimize line speeds
- Quality control accesses historical defect patterns to adjust inspection protocols
- Finance correlates production metrics with waste reduction initiatives
- Sales leverages on-time delivery stats to manage customer expectations
This integration proved transformative for a Colorado microbrewery, where cross-departmental data sharing reduced packaging errors by 34% and improved customer satisfaction scores by 19% within eight months.
Predictive Operational Intelligence
Next-gen systems employ machine learning to anticipate issues before they escalate. By analyzing 17 production variables (including ambient humidity, conveyor speeds, and glass thickness), predictive models achieve 89% accuracy in forecasting bottle breakage events. An Ontario craft brewery piloting this technology reduced packaging waste by $12,000 monthly through preemptive line adjustments during high-risk periods.
FirstStep AI: Bridging Technology and Teamwork
The Operator Logbook Revolution
FirstStep AI’s digital Operator Logbook replaces fragmented whiteboard notes with structured, searchable records capturing:
- Machine performance metrics
- Quality control checkpoints
- Maintenance interventions
- Anomaly documentation
This living system enables seamless knowledge transfer across shifts while providing auditable compliance trails. A recent implementation at a Midwest IPA producer reduced shift handover errors by 68% and improved regulatory audit completion speed by 41%.
Intelligent Shift Handover Protocols
Conclusion: Brewing Success Through Connected Systems
The transition from whiteboards to digital operations management represents more than technological upgrading-it’s a cultural shift toward collaborative excellence. When packaging line operators, quality specialists, and financial analysts share a unified operational picture, they transcend traditional silos to achieve production harmony.
FirstStep AI’s solutions exemplify this evolution by:
- Converting isolated data points into actionable operational intelligence
- Creating accountability through transparent, department-spanning records
- Empowering teams to focus on strategic improvement rather than reactive troubleshooting
In an industry where a single defective bottle can trigger cascading financial and reputational consequences, digital systems provide the connective tissue linking every production facet. Breweries embracing this transformation report 34% faster employee onboarding, 27% fewer customer complaints, and 19% higher line utilization rates-metrics that collectively define competitive advantage in the modern beer market.
The future belongs to facilities recognizing that every shift handover and quality check forms part of an interconnected continuum. By replacing erasable markers with enduring data streams, forward-thinking breweries are crafting a new legacy-one where operational transparency flows as freely as their finest brews.