Case Study:
AB InBev
Improving quality, efficiency, and reducing costs across AB InBev’s production lines.
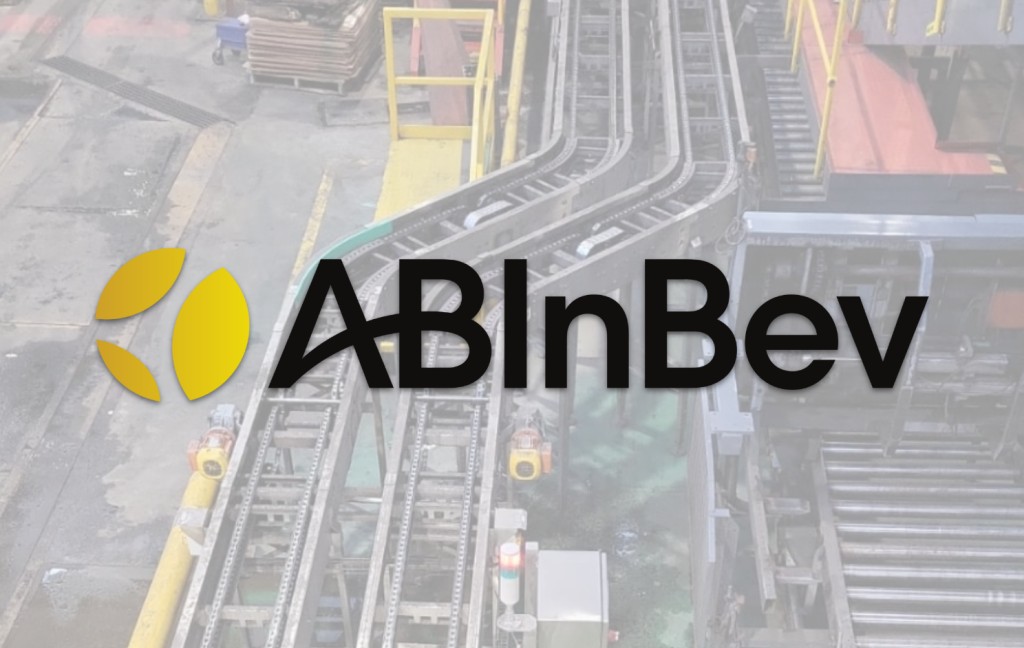
AB InBev Case Study: Optimizing Production Efficiency
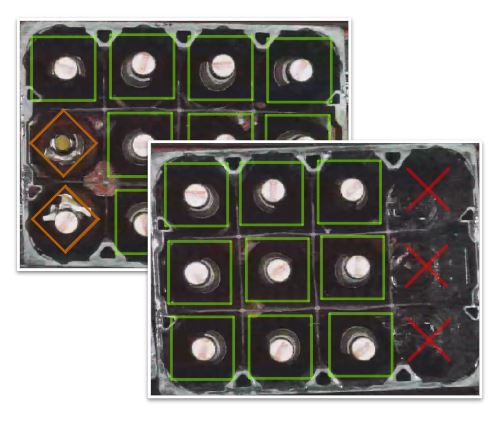
🏭 Operational Challenge
ABI previously relied on manual crate checks and unreliable in-line sensors, which fell short of the accuracy needed by QA and accounting teams. Additionally, as ABI transitions from crate-count to bottle-count reporting, their previous crate counters offer no support for this shift.
☑️ Applicable Solutions
- ☑️ Vision Suite: Crate Inspector
- ☑️ Vision Suite: Closed Loop Rejection
- ☑️ Operations Suite: Shift Reports
- ☑️ Operations Suite: Operator Logbook
- ☑️ Predictive Analytics: Thermal & Condition Monitoring
💰 Business Impact
- 💰 Eliminates manual QC bottlenecks
- 💰 Enables rapid brand changeovers
- 💰 Enhances compliance and traceability
- 💰 Optimizes maintenance scheduling
📊 Quantifiable Metrics
- 📊 99.99% inspection accuracy at 7,200 crates/hour
- 📊 99.99% rejection accuracy on conveyors at 1m/s
- 📊 Total crates scanned: ~750,000 (monthly / line)
- 📊 Total bottles scanned: ~8.8 million (monthly / line)
- 📊 Total bottles scanned: ~2.1 billion (annually, 30 lines)
ROI Highlights
7,200 Crates / Hour
Handles single or dual conveyors at up to 1 m/s.
99.99% Inspection Accuracy
Detects bottle presence, fill level, and crate defects in real time.
99.99% Rejection Accuracy
Rejects crates not meeting quality standards. No sensors required.
83,000 Crates Rejected
Crates automatically rejected per year on average (per line).
$415k Avoided Loss
Estimated savings (per line) from accurate rejection and inspection.
$12.5M Avoided Loss
Annual savings from automated inspection (across 30 lines).