Use Case:
Packaging
Solutions for the discrete high-speed packaging industry.
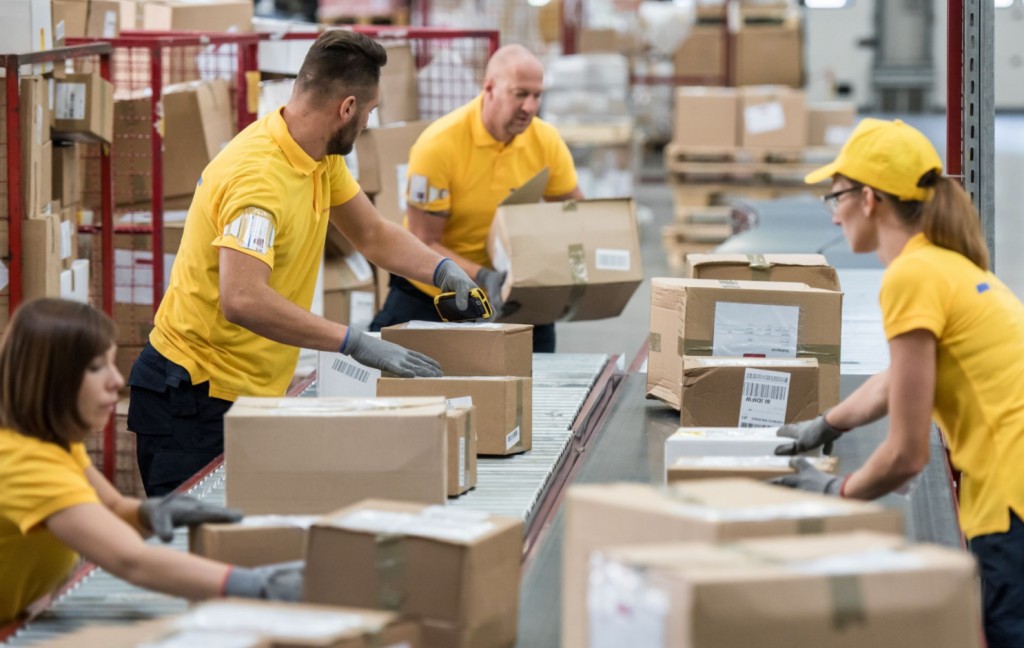
Quality Assurance: Crate & Bottle Inspection

🏭 Operational Challenge
Packaging lines face intense pressure: rapid throughput, strict brand compliance, and minimal room for error. Manual QC on bottling lines struggles to keep pace, leading to missed defects, glass breakage risks, and inconsistent documentation. Frequent brand changeovers cause downtime, and scaling inspection without disrupting production remains a major challenge.
☑️ Applicable Solutions
- ☑️ Vision: Crate Inspector
- ☑️ Operations: Logbook
- ☑️ Operations: Shift Handover
💰 Business Impact
- 💰 Eliminates manual QC bottlenecks
- 💰 Enables rapid brand changeovers
- 💰 Generates shift and daily reports
- 💰 Enhances compliance and traceability
📊 Quantifiable Metrics
- 📊 7,200 crates/hour throughput
- 📊 99.99% inspection accuracy
- 📊 0 additional operators needed
- 📊 <1s defect detection + alert latency
Predictive Maintenance: Thermal Monitoring
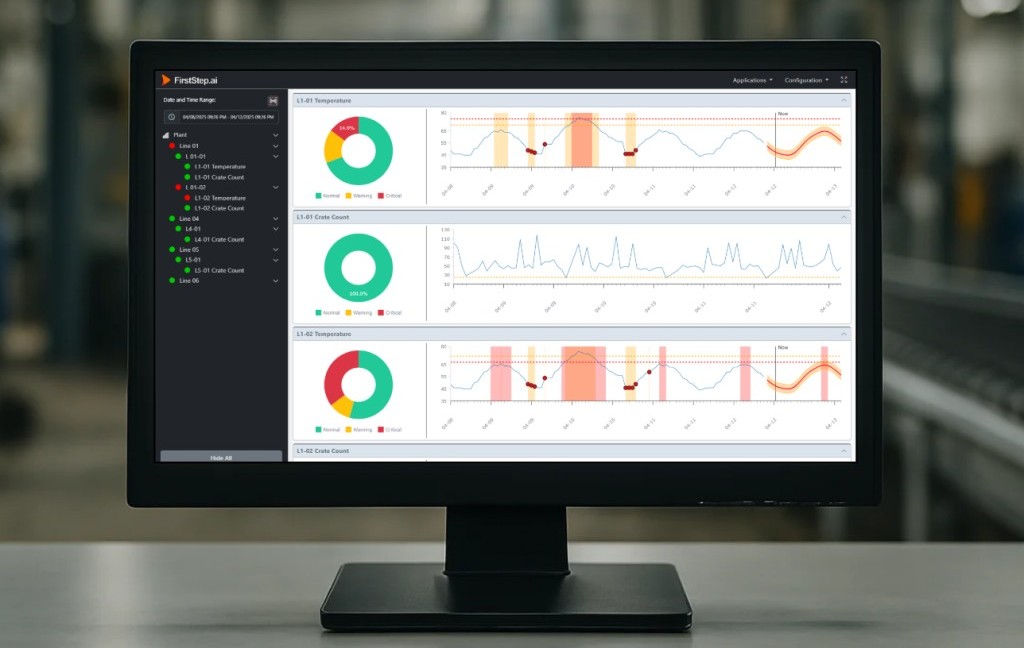
🔮 Description
FirstStep.ai’s Predictive Analytics monitors Crate Inspector temperatures in real time. Using historical trends and AI models, the system forecasts overheating risk with up to 24 hours’ notice, providing early warnings before failures occur.
☑️ Key Features
- ☑️ Real-time temperature monitoring
- ☑️ Warning + critical thresholds
- ☑️ 24-hour predictive forecasts
- ☑️ Operator notifications
- ☑️ Works with existing Vision deployments
⭐ Unique Selling Points
- ⭐ Avoids thermal shutdowns
- ⭐ Fully autonomous with AI learning
- ⭐ No operator intervention required
- ⭐ Protects line uptime
💰 Business Impact
- 💰 Prevents unexpected equipment failure
- 💰 Reduces emergency maintenance calls
- 💰 Enhances production continuity